views
Explosion proof LED lights are critical safety tools designed to prevent ignition in volatile environments where flammable gases, dust, or vapors are present. From oil refineries to chemical plants, these specialized fixtures ensure reliable illumination while mitigating explosion risks.
1. How Explosion Proof LED Lights Work
Unlike standard LED lights, explosion proof LED lights feature robust construction and advanced engineering. Their housings are crafted from materials like cast aluminum or stainless steel, which withstand extreme pressure and contain internal sparks. Sealed gaskets and tempered glass lenses prevent flammable substances from entering the fixture, while thermal management systems dissipate heat safely.
These lights also use intrinsically safe circuits that limit electrical energy to levels below what’s needed to ignite hazardous atmospheres. For example, in oil and gas facilities, this design prevents a single fault from triggering catastrophic events.
2. Key Advantages Over Traditional Lighting
-
Safety Compliance: Meets strict standards like ATEX, IECEx, and UL, ensuring suitability for Zone 1 and Zone 2 hazardous areas.
-
Energy Efficiency: Consumes 50–70% less energy than halogen or HID lamps, reducing operational costs.
-
Durability: Resists corrosion, impacts, and water ingress (IP66/67 ratings), ideal for offshore rigs or mining sites.
-
Longevity: Lasts up to 100,000 hours, minimizing maintenance in hard-to-access locations.
A study projects the global explosion proof LED market to grow at 8.5% CAGR through 2030, driven by stricter safety regulations and industrial automation.
3. Applications Across Industries
Explosion proof LED lights are indispensable in high-risk sectors:
-
Oil & Gas: Illuminates drilling platforms and refineries where methane or hydrogen sulfide may accumulate.
-
Mining: Provides reliable lighting in coal dust-heavy tunnels without sparking explosions.
-
Chemical Processing: Withstands corrosive fumes in storage tanks or production lines.
-
Wastewater Treatment: Operates safely in methane-rich environments near digesters.
Portable explosion proof LED lights are also used for emergency repairs or inspections in confined spaces.
4. Choosing the Right Fixture
A. Certifications Matter
Verify compliance with regional standards. For instance, ATEX governs EU markets, while NEC Article 500 applies in North America.
B. Lumens and Beam Angle
High-bay areas (e.g., warehouses) require 20,000+ lumens and wide beam angles, whereas task lighting in labs benefits from focused beams.
C. Smart Features
Opt for models with motion sensors or IoT connectivity to enable remote monitoring and adaptive brightness, enhancing energy savings.
5. Installation and Maintenance Best Practices
-
Wiring Safety: Use conduit seals and explosion proof junction boxes to prevent arc faults.
-
Mounting: Secure fixtures with anti-vibration brackets in areas prone to mechanical stress, like shipyards.
-
Routine Checks: Inspect seals and gaskets annually for wear. Clean lenses with non-abrasive solutions to maintain light output.
Common mistakes include using non-rated dimmers (causing flickering) or ignoring thermal management, which shortens LED lifespan.
6. Future Trends Shaping the Industry
-
Solar Integration: Off-grid explosion proof LED systems for remote oil fields, reducing reliance on generators.
-
Self-Diagnostic Systems: AI-powered sensors detect faults like loose wiring before failures occur.
-
Lightweight Materials: Carbon fiber housings for easier installation in offshore wind farms.
Manufacturers are also focusing on modular designs, allowing users to replace components (e.g., drivers) without discarding entire fixtures.
Conclusion
Explosion proof LED lights are more than illumination tools—they’re lifesaving investments. By prioritizing certified, energy-efficient models and adhering to installation protocols, industries can enhance safety while cutting long-term costs. As technology evolves, smart and sustainable designs will redefine hazard-prone workspaces, proving that innovation and safety go hand in hand.
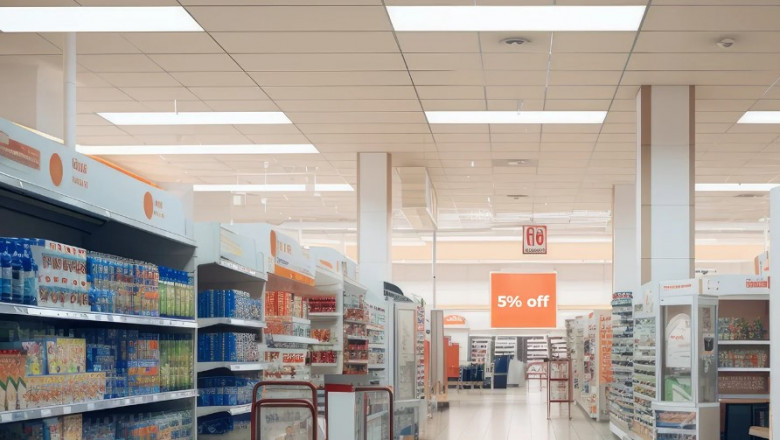

Comments
0 comment